Understanding the Differences Between MDF, HDF, and HDMR: Which One is Right for You?
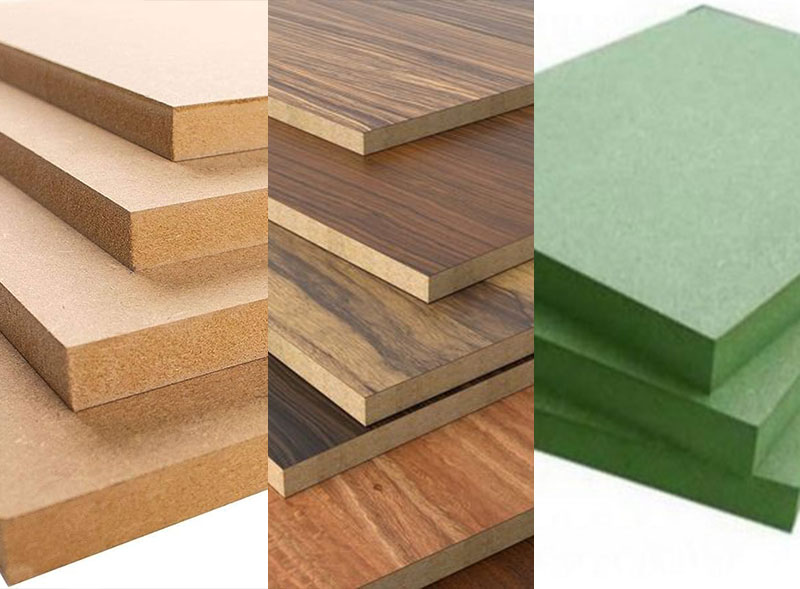
In woodworking and construction, selecting the right material is pivotal to the success and durability of any project. Medium Density Fiberboard (MDF), High Density Fiberboard (HDF), and High Density Moisture Resistant Board (HDMR) stand as prominent choices, each offering distinct characteristics and applications. In this guide, we’ll delve into the unique features of MDF, HDF, and HDMR, helping you make an informed decision on which one suits your requirements best.
Medium Density Fiberboard (MDF):
MDF, a versatile and cost-effective option, is composed of wood fibers bonded together with resin under high pressure and temperature.
Known for its smooth and consistent surface, MDF finds its forte in applications requiring intricate designs and finishes. It excels in indoor projects such as cabinetry, shelving, furniture components, and decorative molding. The homogeneous structure of MDF allows for precise cuts, easy machining, and painting, making it an ideal choice for interior woodworking projects where a flawless finish is paramount. Despite its versatility and affordability, MDF is susceptible to moisture and does not perform well in areas prone to humidity. Hence, it’s crucial to assess the project’s environment before
opting for MDF.
High Density Fiberboard (HDF):
Stepping up in density and durability, HDF is engineered for high-strength applications demanding toughness and stability.
Composed of finely ground wood fibers compressed under high pressure, HDF boasts greater density than MDF, resulting in improved strength and load-bearing capabilities. HDF excels in flooring, sub-flooring, and areas that require impact resistance, such as furniture components, panels, and heavy-duty structural elements. HDF’s higher density makes it less susceptible to moisture compared to MDF, yet it’s essential to note that HDF isn’t entirely waterproof. It’s imperative to consider the specific environment and application when choosing HDF.
High Density Moisture Resistant Board (HDMR):
Designed to withstand moisture and humidity, HDMR elevates the game further by combining high density with moisture resistance.
Engineered for areas prone to dampness, such as kitchens, bathrooms, and spaces exposed to high humidity, HDMR offers superior dimensional stability and resistance to moisture-related issues like swelling and warping. HDMR’s composition, much like HDF, involves tightly compressed wood fibers. However, its specialized construction with moisture-resistant properties makes it an ideal choice for
environments where other materials might falter due to moisture exposure.
Basic Differences in Features:
Feature | MDF (Medium Density Fiberboard) |
HDF (High Density Fiberboard) |
HDMR (High Density Moisture Resistant Board) |
Density | Medium | High | High |
Composition | Wood fibers bonded with resin |
Finely ground wood fibers |
Compressed wood fibers with moisture resistance additives |
Strength | Moderate | High | High |
Load-Bearing Capacity |
Limited | Greater | Greater |
Surface Texture | Smooth and consistent |
Smooth and dense | Smooth and dense with moisture resistance |
Applications | Interior woodworking, cabinetry, furniture, decorative elements |
Flooring, sub-flooring, furniture components, heavy-duty structural elements |
Areas prone to moisture such as kitchens, bathrooms, humid environments |
Machinability | Cuts easily, easy machining and painting |
Precise cuts, suitable for flooring and structural elements |
Precision cutting, resistant to swelling and warping due to moisture |
Vulnerability to Moisture |
Susceptible | Less susceptible | Resistant to moisture-related issues |
Ideal Environments |
Dry indoor applications |
Indoor applications requiring higher strength |
Environments prone to humidity and moistur |
Choosing the Right Option for Your Project:
The selection between MDF, HDF, and HDMR hinges on various factors, including the intended application, environmental conditions, and specific project requirements. To determine the right fit:
1. Consider Application Needs:
Assess the project’s requirements – whether it demands a smooth finish, high load-bearing capacity, or moisture resistance.
2. Evaluate Environmental Factors:
Determine the environmental conditions where the material will be used – consider moisture levels, humidity, and exposure to the elements.
3. Understand Strength and Durability Requirements:
Determine the level of durability, impact resistance, and load-bearing capacity needed for the project.
Conclusion:
In conclusion, while MDF, HDF, and HDMR share similarities in their composition, they cater to distinct needs in woodworking and construction. Whether it’s achieving a flawless finish with MDF, opting for robustness and strength with HDF, or prioritizing moisture resistance with HDMR, each material serves a specific purpose. By understanding their unique attributes and assessing your project’s requirements, you can make an informed choice that aligns perfectly with your woodworking and construction needs.